Breaking Down Operations to Their Fundamental Elements: An Introduction to the Elements Approach
- Umashree
- Apr 7
- 5 min read
In the complex world of distribution operations, clarity is your most valuable asset. When operations become convoluted—as they inevitably do in growing businesses—leaders find themselves making decisions based on incomplete information, managing symptoms rather than causes, and implementing solutions that create new problems elsewhere in the system.
But what if there was a methodical way to cut through this complexity? A first principles approach that breaks down operations to their fundamental building blocks, creating visibility and enabling truly informed decisions?
This is the foundation of the Elements Approach.
Why Traditional Operational Improvement Methods Fall Short
Distribution operations have historically relied on best practices and industry benchmarks to guide improvement efforts. While these approaches offer value, they share a common limitation: they apply solutions that worked in one specific context to entirely different operational environments.
This analogical reasoning—taking what worked elsewhere and applying it to your unique situation—is like trying to fix a Swiss watch with tools designed for a grandfather clock. The tools might be excellent, but they weren't designed for your specific mechanism.
First principles thinking offers a fundamentally different approach.
What Is First Principles Thinking in Operations?
First principles thinking, championed by innovators from Aristotle to Elon Musk, involves breaking down complicated problems into basic elements and then reassembling them from the ground up.
In operations, this means:
Decomposing complex systems into their fundamental elements
Understanding each element's purpose and performance
Evaluating how elements interact and influence each other
Rebuilding solutions based on this elemental understanding
Instead of asking, "What do other companies do?" we ask, "What are the fundamental components of this operation, and how should they work together to achieve our specific goals?"
The Five Elements of Distribution Operations
Through years of analyzing distribution operations across various industries, I've identified five fundamental element categories that form the building blocks of any operation:
1. Physical Elements
These are the tangible components of your operation:
Inventory
Facilities
Equipment
Materials
Physical layouts
Physical elements are often the most visible part of operations but are frequently misunderstood in terms of their relationships and dependencies.
2. Process Elements
These define how work flows through your operation:
Workflows
Procedures
Decision points
Handoffs
Information flows
Process elements determine how physical elements move and transform, acting as the "operating system" of your business.
3. Data Elements
These provide visibility and enable decision-making:
Metrics
KPIs
Reporting structures
Information visibility
Decision support
Data elements translate what's happening in your operation into actionable intelligence. Without properly designed data elements, operations become "invisible" to management.
4. Human Elements
These represent the people dimension of operations:
Skills
Behaviors
Incentives
Communication patterns
Decision-making authority
Human elements often receive the least analytical attention but frequently have the greatest impact on operational performance.
5. Financial Elements
These connect operations to business outcomes:
Cost structures
Pricing mechanisms
Cash flow drivers
Investment priorities
Financial constraints
Financial elements translate operational performance into business results and often dictate the constraints within which operations must function.
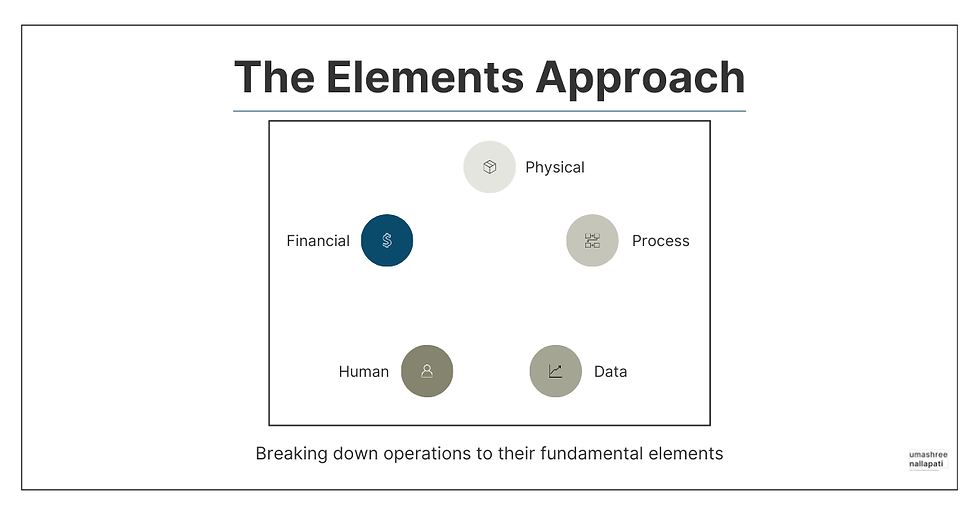
The Element Analysis Framework
Once you've identified your operational elements, the next step is analyzing them through five critical lenses:
Purpose
What is this element's fundamental role in the system? Why does it exist?
Performance
How well is the element fulfilling its purpose? What are its capabilities and limitations?
Connections
How does this element interact with others? What are its dependencies and influences?
Constraints
What limits this element's effectiveness? What are its bottlenecks?
Optimization
How could this element be improved or redesigned to better serve its purpose?
This structured analysis reveals insights that remain hidden in traditional operational reviews. It highlights not just what's happening in your operation, but why it's happening and how elements influence each other.
From Analysis to Synthesis: Rebuilding Better Operations
The true power of elemental decomposition emerges during the rebuilding phase, where you can:
Eliminate unnecessary elements that add complexity without value
Strengthen weak elements that limit system performance
Redesign flawed elements that create persistent problems
Optimize connections between elements to improve flow
Add missing elements that create critical capabilities
Balance the system to ensure sustainable performance
This rebuilding process, grounded in first principles understanding, creates operations that are purpose-built for your specific business goals rather than cobbled together from disparate best practices.
A Case Example: Element Analysis in Action
To illustrate this approach, consider a building materials distributor struggling with inventory accuracy. Traditional approaches might jump directly to cycle counting programs or warehouse management systems.
Using elemental decomposition, however, revealed:
Physical Elements: Inventory was stored in multiple locations without clear boundaries
Process Elements: Receiving and put-away procedures lacked verification steps
Data Elements: Inventory metrics focused on total value rather than accuracy
Human Elements: Staff incentives rewarded speed over accuracy
Financial Elements: Accounting practices masked the true cost of inaccuracy
This comprehensive understanding led to targeted improvements across all elements, resulting in sustainable 98%+ inventory accuracy where previous initiatives had failed.
Implementing the Operational Elements Approach in Your Business
Ready to apply this approach to your operations? Here are the first steps:
Select a specific operational area with clear boundaries for your initial analysis
Identify all elements within that area using the five categories
Map relationships between elements to understand dependencies
Analyze each element through the five analytical lenses
Look for patterns of strength, weakness, and opportunity
Develop a rebuilding plan that addresses root causes, not symptoms
This methodical approach transforms operational problem-solving from reactive firefighting to strategic system design.
The Journey to Operational Clarity
Elemental decomposition isn't a quick fix. It's a fundamental shift in how you understand and improve operations. The journey requires intellectual curiosity, analytical discipline, and a willingness to question established practices.
But the rewards are substantial: operations that continuously adapt to business needs, decisions based on fundamental understanding rather than guesswork, and sustainable performance that doesn't depend on constant intervention.
In the coming weeks, we'll dive deeper into each element category, exploring practical applications and implementation frameworks. For now, I encourage you to look at one operational challenge you're facing and ask: "What are the fundamental elements at play here, and how might understanding them change my approach?"
The path to operational excellence begins with clarity. And clarity begins with breaking down complexity to its essential elements.
Are you interested in learning more about applying the Elements Approach to your operations? Download our free "Operational Elements Identification Guide" to get started.
Stay Informed with Elemental Insights
This introduction to the Elements Approach is just the beginning. Each week, our "Elemental Insights" newsletter delivers practical frameworks, implementation guidance, and real-world applications directly to your inbox.
Subscribe now to receive:
The "Mental Model of the Week" with operational applications
Exclusive subscriber-only resources and tools
Step-by-step implementation guidance
Early access to new frameworks before they're published
Join the growing community of operations leaders who are transforming complexity into clarity through first principles thinking.
Your operational excellence journey begins with a single element. Take the first step today.
Comments